China CNC Lathe Machining Parts Manufacturers: An In-Depth Analysis
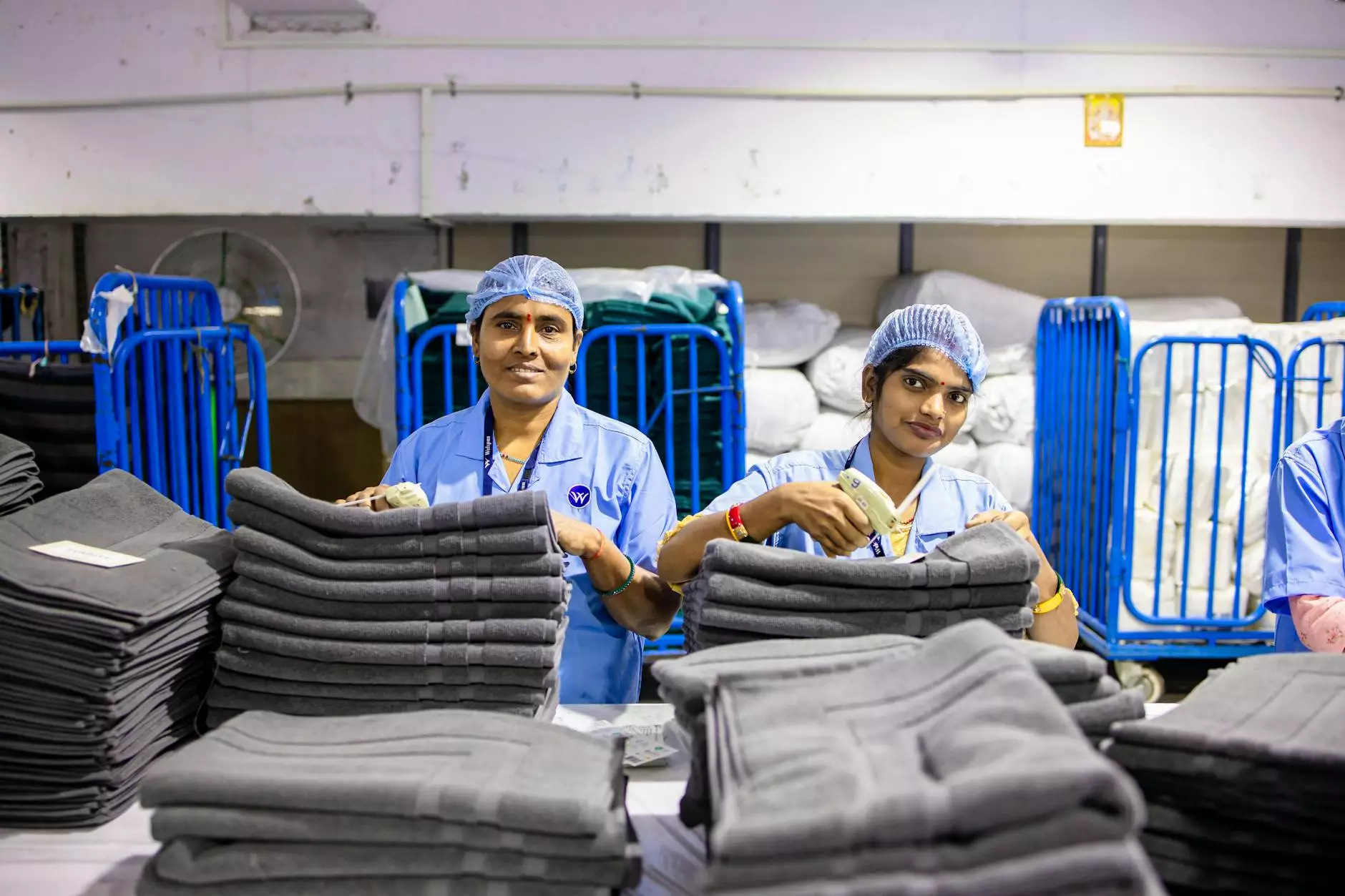
The global landscape of manufacturing has undergone significant transformations over the past few decades, and at the heart of this evolution is the rise of CNC (Computer Numerical Control) technology. Among the leading players in CNC machining are China CNC lathe machining parts manufacturers, known for their advanced technology, cost-effectiveness, and exceptional production capabilities. In this article, we will delve into the intricacies of these manufacturers, exploring their processes, advantages, and how they effectively serve diverse industries worldwide.
Understanding CNC Lathe Machining
CNC lathe machining involves using computerized controls to operate lathes, which are machines designed to shape materials such as metal, plastic, and wood. The process is highly precise, allowing manufacturers to create intricate components with remarkable accuracy. In China, CNC lathe machining is a cornerstone of the manufacturing sector, enabling the production of parts ranging from simple screws to complex engine components.
Importance of CNC Machining in Modern Manufacturing
The demand for precise, high-quality components has surged, and CNC machining offers solutions that traditional machining methods cannot match. Some of the key benefits include:
- Precision and Accuracy: CNC machines can produce parts with tolerances as tight as ±0.001 inches.
- Efficiency: The automation of machining processes reduces lead times, allowing manufacturers to fulfill larger orders swiftly.
- Flexibility: CNC programming allows for quick adjustments to designs, accommodating varying client needs without extensive re-tooling.
- Consistency: Once a design is programmed, CNC machines produce identical parts, ensuring uniformity across large production runs.
Key Applications of CNC Lathe Machining
China CNC lathe machining parts manufacturers cater to a vast array of industries, including:
- Aerospace: Producing lightweight, durable components that meet stringent safety standards.
- Automotive: Creating intricate parts such as engine casings, gears, and brackets.
- Medical: Manufacturing precision instruments and implants required for healthcare applications.
- Electronics: Producing complex enclosures and components for various electronic devices.
Why Choose China CNC Lathe Machining Parts Manufacturers?
When considering sourcing CNC lathe machining parts, many companies turn to Chinese manufacturers due to several compelling reasons:
Cost-Effectiveness
One of the primary advantages of working with China CNC lathe machining parts manufacturers is the significant cost savings. Labor and overhead costs are typically lower in China, allowing manufacturers to offer competitive pricing without compromising quality. This is particularly beneficial for small to medium-sized enterprises (SMEs) looking to scale their production costs.
Access to Advanced Technology
Chinese manufacturers continually invest in innovative technologies, enhancing their CNC machining capabilities. Many facilities employ state-of-the-art equipment and software, ensuring that they remain at the forefront of manufacturing trends. This technological edge translates to higher quality products and more efficient production processes.
Skilled Workforce
China boasts a vast pool of skilled engineers and technicians adept in CNC machining. These professionals are trained in the latest technologies and practices, contributing to the overall quality and efficiency of the manufacturing process. As a result, companies can rely on the expertise of their manufacturing partners.
Robust Supply Chain
China has established a well-developed supply chain network, making it easier for manufacturers to procure materials and components. This efficiency reduces lead times and helps ensure on-time delivery of products, thereby enhancing customer satisfaction.
Evaluating Quality in CNC Machining
Quality assurance is paramount in CNC machining. Here are several criteria to consider when evaluating potential manufacturers:
- Certifications: Look for ISO 9001 certifications or industry-specific accreditations that indicate adherence to high standards of quality control.
- Production Capacity: Assess the manufacturer's ability to meet your demands in terms of volume and complexity of parts.
- Material Capabilities: Ensure they can work with the specific materials required for your parts, whether metals, plastics, or composites.
- Customer Testimonials: Research reviews and case studies to gauge the experiences of previous clients.
Common CNC Machining Processes
China CNC lathe machining parts manufacturers utilize various processes to create components, including:
Turning
Turning is the most common method employed in CNC lathe machining, where a rotating workpiece is shaped by a stationary cutting tool. This technique is ideal for producing cylindrical objects such as shafts and rings.
Milling
Milling involves the use of rotating cutters to remove material from a stationary workpiece. This process can create various shapes and features, making it suitable for complex components.
Drilling
Drilling is often combined with turning and milling to create holes in machined components. CNC drills provide high accuracy and consistency, essential for parts requiring precise hole placements.
Quality Control Mechanisms
To guarantee the quality of produced parts, Chinese manufacturers employ several quality control mechanisms:
- Incoming Material Inspection: All raw materials are thoroughly inspected for defects before they enter the production line.
- In-Process Inspection: Regular checks during the machining process help identify any deviations from specifications early, enabling corrective actions.
- Final Quality Checks: Completed parts undergo rigorous testing to ensure they meet customer expectations and industry standards.
Challenges Faced by CNC Manufacturers in China
While there are numerous advantages to working with China CNC lathe machining parts manufacturers, there are also challenges that companies must navigate:
Intellectual Property Risks
Intellectual property theft can be a concern when partnering with overseas manufacturers. It’s crucial to establish legal agreements that protect sensitive designs and technologies.
Quality Variability
Not all manufacturers maintain the same quality standards. Due diligence is necessary to select reliable partners who prioritize quality assurance throughout the production process.
Communication Barriers
Language differences can lead to misunderstandings. Clear communication channels and possibly the use of a bilingual project manager can help mitigate these issues.
Future Trends in CNC Machining
The CNC machining landscape is continuously evolving, with several trends shaping its future:
- Increased Automation: The integration of more automated processes is expected to enhance efficiency and reduce production costs.
- Adoption of Industry 4.0: The shift towards smart manufacturing through IoT (Internet of Things) technologies promises greater connectivity and data utilization.
- Sustainable Practices: Environmental concerns are driving manufacturers to adopt greener practices, such as using recycled materials and reducing waste.
Conclusion
China CNC lathe machining parts manufacturers have solidified their place in the global manufacturing industry. Their capabilities, combined with the benefits of cost-effectiveness and cutting-edge technology, enable them to produce high-quality components across various sectors. By understanding the intricacies of CNC machining, businesses can make informed decisions when sourcing parts and leverage the strengths of these manufacturers to enhance their production processes.
As you explore potential partnerships in CNC machining, consider the rich history, expertise, and innovation that these manufacturers offer. China continues to lead the way in CNC lathe machining, positioning itself as a crucial player in the future of global manufacturing.
Explore Our Services at DeepMould.net
If you’re looking for a trusted partner in metal fabrication or CNC machining, look no further than DeepMould.net. Our commitment to quality, precision, and customer satisfaction makes us a preferred choice among industry leaders.