The Essential Role of CNC Precision Machining Suppliers in Modern Manufacturing
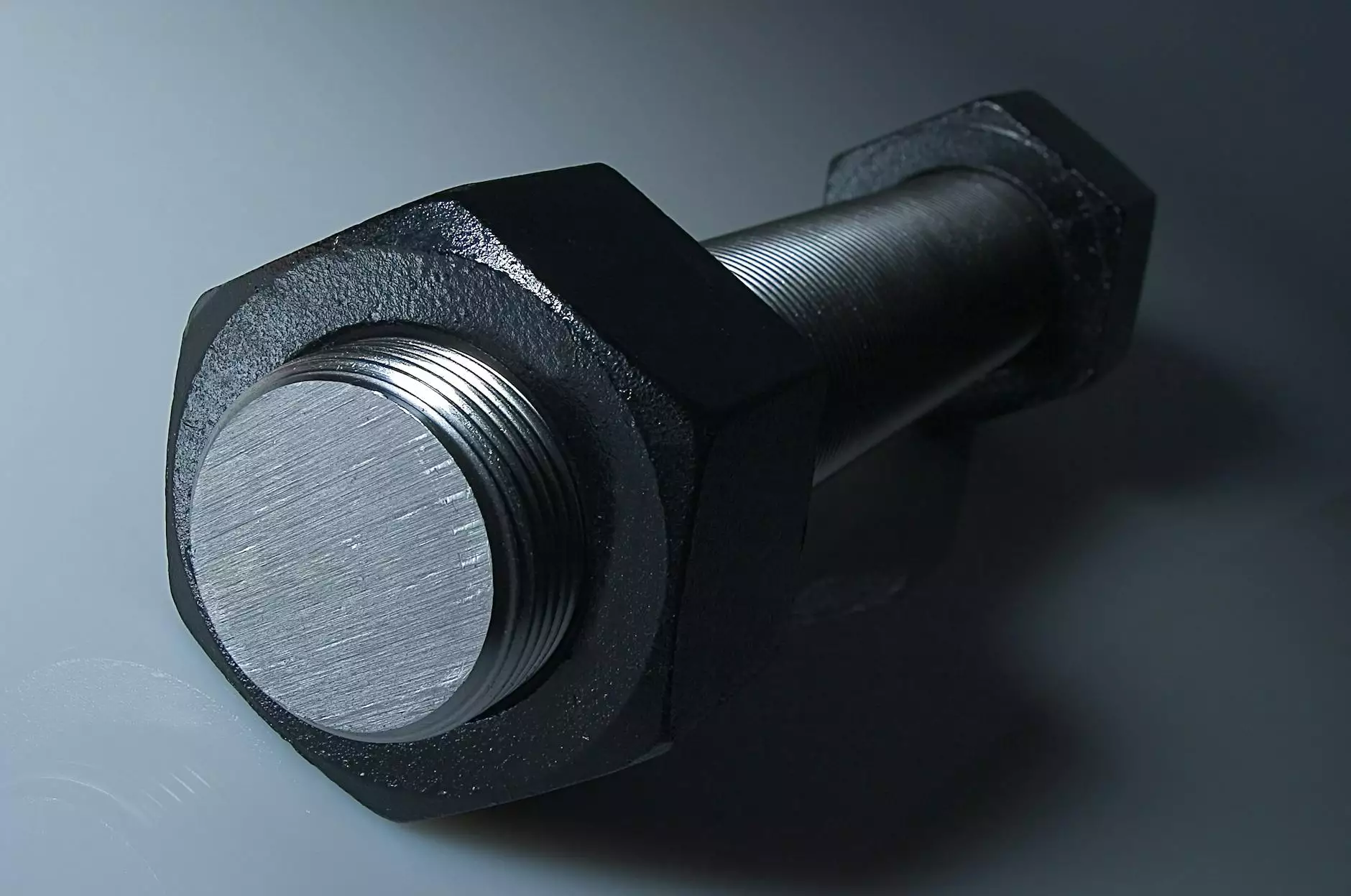
CNC precision machining has become a cornerstone of modern manufacturing, offering unparalleled accuracy, efficiency, and customization. As businesses increasingly rely on intricate metal components, the demand for reliable cnc precision machining suppliers has surged. This article delves into the significance of this technology, its benefits, and how to select the right supplier for your needs.
Understanding CNC Precision Machining
CNC, or Computer Numerical Control, refers to the use of computers to control machine tools in manufacturing. This technology allows for the automated production of parts, significantly enhancing precision and reducing human error. CNC precision machining encompasses various processes, including milling, turning, grinding, and electrical discharge machining (EDM).
The Advantages of CNC Precision Machining
- High Precision: CNC machines can produce parts to tolerances as tight as ±0.001 inches, ensuring components fit perfectly.
- Efficiency and Speed: Automated processes drastically reduce manufacturing time, leading to quicker turnaround times.
- Complex Geometries: CNC machining can create intricate designs that would be impossible or highly impractical with traditional methods.
- Scalability: Once programmed, CNC machines can produce large volumes of identical parts with consistent quality.
- Reduced Waste: Advanced machining techniques optimize material usage, lowering production costs and environmental impact.
Why Choose a Trusted CNC Precision Machining Supplier?
Partnering with a reputable cnc precision machining supplier is crucial for businesses that require high-quality metal parts. Here’s why working with professionals matters:
Quality Assurance
A trusted supplier will adhere to rigorous quality control standards, ensuring that every part meets specifications. Quality assurance processes might include:
- ISO Certification: Compliance with international standards demonstrates a commitment to quality and reliability.
- Continuous Monitoring: Regular inspections and testing of parts during production guarantee consistency.
Expertise and Experience
With years of experience in the industry, a quality supplier will possess the knowledge required to tackle complex machining projects. They can provide valuable insights into design optimization and material selection, which can enhance the performance of your components.
Key Factors to Consider When Selecting a CNC Precision Machining Supplier
When choosing a cnc precision machining supplier, several factors should be taken into account to ensure you select the right partner for your business needs:
1. Machines and Technology
The capabilities of the supplier's machinery are paramount. Look for suppliers that invest in advanced CNC technology, such as:
- Multi-Axis Machining: This allows for more complex shapes and reduces the need for multiple setups.
- Automation: Automated loading and unloading can enhance efficiency and reduce labor costs.
2. Materials and Capabilities
Ensure the supplier is experienced in machining the specific materials you require, whether they be:
- Metals: Aluminum, steel, titanium, and alloys.
- Plastics: Various types including ABS, polycarbonate, and nylon.
3. Customer Support and Communication
Effective communication is essential for project success. A good supplier should offer:
- Responsive Customer Service: Quick responses to inquiries and concerns.
- Project Management: Dedicated personnel to oversee your project and provide updates.
4. Pricing and Lead Times
While cost should not be the sole factor, it is important to consider pricing in relation to your budget. Additionally, ask about:
- Lead Times: Understand their typical turnaround times for production.
- Bulk Order Discounts: Inquire about pricing structures for larger orders.
The Future of CNC Precision Machining
The landscape of CNC precision machining is continuously evolving, driven by advancements in technology and changing market demands. Key trends include:
1. Integration of IoT and Smart Manufacturing
The Internet of Things (IoT) is increasingly being integrated into manufacturing processes, allowing for real-time data collection and analysis. This connectivity can enhance productivity and reduce downtime through predictive maintenance.
2. The Rise of Additive Manufacturing
While CNC machining is traditionally subtractive, the rise of additive manufacturing (3D printing) offers complementary solutions for creating complex geometries. Many suppliers are exploring hybrid technologies that combine both methods.
Deepmould.net: Your Premier CNC Precision Machining Supplier
At Deepmould.net, we pride ourselves on being a leading cnc precision machining supplier. Our commitment to quality, state-of-the-art technology, and customer-centric approach ensures your projects are in capable hands. Here’s what we offer:
- Comprehensive Machining Services: From prototyping to high-volume production, we cover all aspects of CNC machining.
- Diverse Material Capabilities: We work with a wide range of materials, ensuring the perfect match for your specifications.
- Expert Consultation: Our team of experienced engineers is available to assist you in optimizing designs and manufacturing strategies.
Conclusion
CNC precision machining is an indispensable part of contemporary manufacturing, and selecting the right cnc precision machining supplier can make all the difference in your project’s success. By understanding the technology, the importance of quality, and the key factors in choosing a supplier, businesses can make informed decisions that lead to long-term partnerships and exceptional results. Connect with us at Deepmould.net to see how we can help elevate your production capabilities.