The Integral Parts of a CNC Lathe and Their Functions
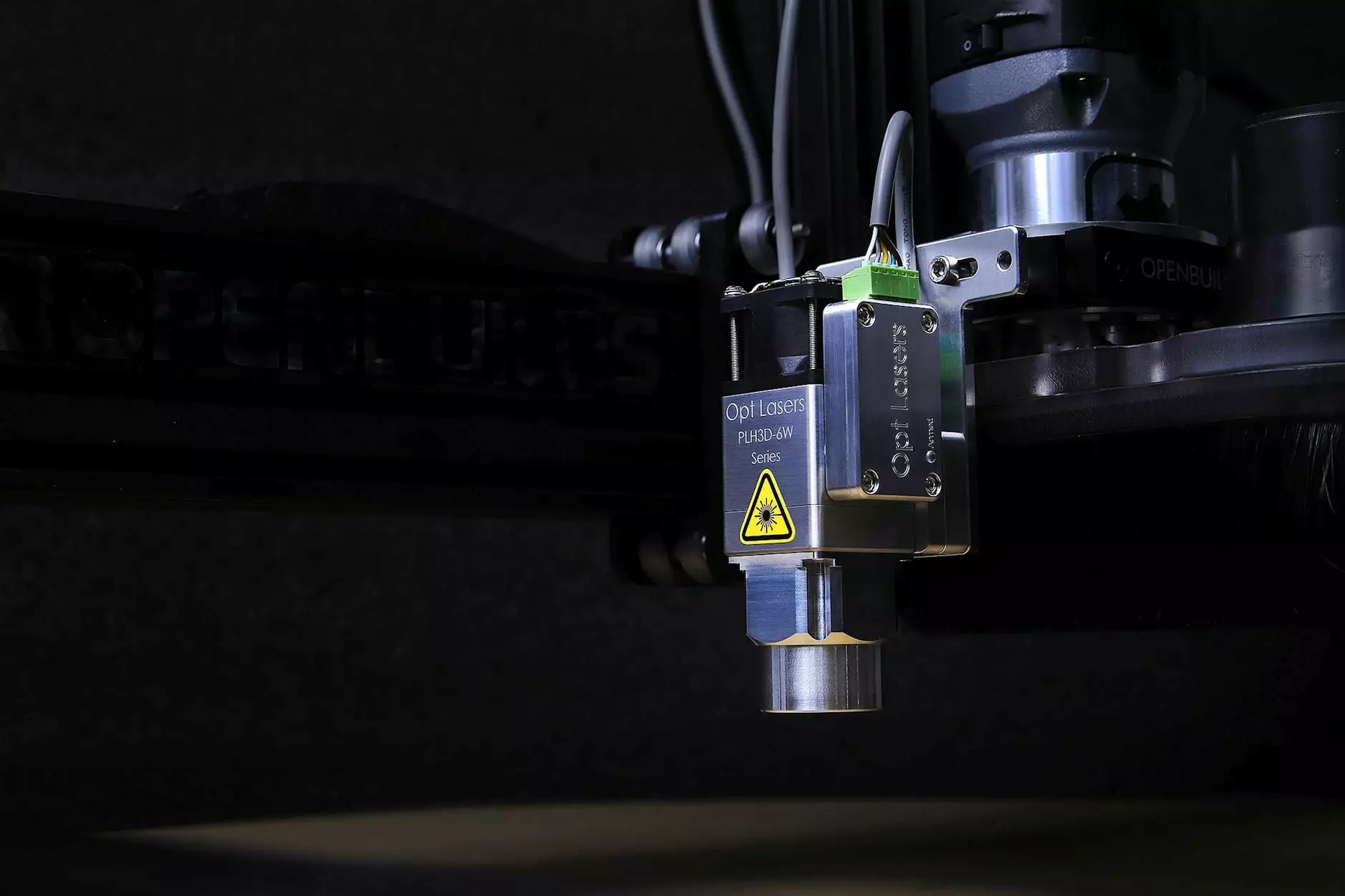
A CNC lathe stands as one of the most pivotal machines in modern metal fabrication and machining. Understanding the parts of a CNC lathe is crucial for those involved in manufacturing processes, whether you are an operator, engineer, or business owner in the metal fabrication industry. In this comprehensive guide, we will delve into each component and highlight their significance in achieving precision and efficiency in manufacturing. At deepmould.net, we pride ourselves on utilizing cutting-edge CNC technology to enhance the metal fabrication process.
1. What is a CNC Lathe?
A CNC lathe is a computer-controlled machine used to shape and cut materials, such as metal, into specific forms. Through programmable commands, these machines can perform various operations, including turning, facing, drilling, and threading. Unlike traditional lathes that require manual input, CNC lathes automate these tasks, increasing precision and reducing production time.
2. Key Components of a CNC Lathe
Understanding the specific parts of a CNC lathe will enable operators and engineers to optimize machine performance. Below, we outline the essential components:
2.1. Bed
The bed is the sturdy frame of the CNC lathe that supports all other components. Typically made of cast iron or steel, the bed must maintain rigidity to absorb vibrations during machining operations, ensuring consistent precision.
2.2. Headstock
The headstock houses the primary spindle, which is responsible for rotating the workpiece. It contains critical components such as the motor, gears, and pulleys that allow for variable speed control. The headstock's precision is paramount for achieving accurate cuts and finishes.
2.3. Tailstock
Situated opposite the headstock, the tailstock provides additional support for longer workpieces. It can be adjusted to various positions along the bed and often includes a quill that can be used for drilling operations. This component enhances stability, particularly when machining lengthy or tapered parts.
2.4. Carriage
The carriage is a mobile assembly that moves along the bed. It includes the cross slide and the tool post, allowing the operator to adjust the tool's position relative to the workpiece. The carriage's movement is controlled remotely through the CNC system, enabling precise positioning and shaping.
2.5. Tool Post
The tool post holds the cutting tools in place. A robust tool post enhances stability and accuracy when machining. Modern CNC lathes often feature turret tool posts, allowing multiple tools to be mounted and quickly accessed, thus improving efficiency.
2.6. Chuck
The chuck is a clamping device that securely holds the workpiece during machining. It can be a three-jaw or four-jaw chuck, depending on the shape and size of the workpiece. The chuck's gripping capacity is critical for achieving uniform cuts and finishes.
2.7. Control Panel
The control panel is the interface through which operators program the CNC lathe. This panel allows for the input of design specifications, tooling instructions, and machine operations. The sophistication of the control software can dramatically impact machining capabilities, making it a vital part of modern CNC lathes.
2.8. Linear Guides
Linear guides facilitate smooth motion of the carriage and other moving parts. These components reduce friction and enhance accuracy during cutting operations. High-quality linear guides are essential for maintaining the machine’s longevity and performance.
2.9. Servo Motors
Servo motors are crucial for driving the movements of the CNC lathe. They convert electrical energy into mechanical movement, allowing for precise control of speed and position. The quality and precision of servo motors significantly influence operational efficiency and product quality.
2.10. Power Supply
The power supply converts electrical energy into the voltage and current levels necessary for the lathe's operation. A reliable power supply ensures consistent performance and reduces the risk of interruptions during machining processes.
3. How Each Component Works Together
Each part of the CNC lathe collaborates in a finely tuned manner to accomplish complex machining tasks. The headstock rotates the workpiece while the carriage moves the tools into position. The tailstock provides additional support, particularly for longer pieces. The control panel relays precise instructions, allowing the entire system to execute cuts with unparalleled accuracy.
4. The Importance of CNC Lathes in Metal Fabrication
CNC lathes play a significant role in modern metal fabrication. Their versatility allows for the manufacturing of various components, from small precision parts to large industrial machinery. Some key benefits of using CNC lathes in metal fabrication include:
- Enhanced Precision: CNC lathes operate with high precision, ensuring that components are produced to exact specifications.
- Increased Efficiency: Automated processes reduce production time and increase throughput, leading to greater operational efficiency.
- Consistent Quality: The repeatability of CNC machining ensures that each part produced conforms to the desired quality standards.
- Complex Geometries: CNC lathes can create intricate shapes and features that would be difficult or impossible to achieve manually.
- Reduced Labor Costs: With automation, fewer skilled operators are needed, reducing overall labor costs.
5. Maintenance of CNC Lathe Parts
To keep a CNC lathe functioning optimally, regular maintenance of its parts is essential. Here are some maintenance tips:
- Regular Lubrication: Ensure all moving parts are regularly lubricated to reduce friction and wear.
- Alignment Checks: Periodically check the alignment of the bed, headstock, and tailstock to maintain accuracy.
- Cleaning: Keep the machine clean from chips, dust, and debris to prevent contamination and ensure smooth operation.
- Software Updates: Regularly update the CNC software to benefit from improvements and enhanced functionalities.
- Inspection: Conduct routine inspections of key components such as the spindle, bearings, and electrical systems for signs of wear or damage.
6. Conclusion
In conclusion, a comprehensive understanding of the parts of a CNC lathe is vital for anyone involved in the metal fabrication industry. Each component plays a unique role in enhancing the efficiency, precision, and quality of the manufacturing process. At deepmould.net, we leverage our expertise in CNC technology to provide unparalleled metal fabricating services. By investing in high-quality CNC lathes equipped with advanced components, businesses can thrive in a competitive marketplace, ensuring customer satisfaction and operational excellence.
7. Further Resources
For those looking to deepen their knowledge about CNC machining and lathes, consider exploring the following resources:
- CNC Association - Industry Resources
- Machine Tool Trade Publications
- Industry Week - Insights and Innovations
- DeepMould Blog - Tips and Trends in Metal Fabrication
By understanding and mastering the intricacies of CNC lathes, professionals in the metal fabrication sector can ensure the durability and productivity of their operations, leading to sustainable growth and success.